Last Updated on January 5, 2021
Considering materials like slate, wood, concrete and other products like asphalt, sheet metal, steel and plastic to synthetic, there seem to be more types and styles of roofing to choose from today than ever before.
Roofing Comparison Chart
Roofing Shingles Warranty Life Expectancy* Average Cost Installed*
3 Tab Shingles
Architectural Shingles
Designer Shingles
Impact Rated Shingles
Metal Shingles
Stone Coated Shingles
Synthetic Shingles
- Is the average life performance time that Cook Roofing Co has seen in real life field conditions. Conditions that effect performance of shingles, are Weather and Climate Conditions, Roof Maintenance, Proper Installations, Roof Flashings, and proper roof ventilation
- Average cost is on a per Square 10*10 Area and is an assumption and should never be used as a true estimate. Existing Roof Conditions and other factors will cause the number to go up or down.
Important Note:
Roofing Product Standards
ASTM’s roofing standards are instrumental in specifying, testing, and evaluating the dimensional, mechanical, and performance requirements of various forms of roofing systems. These systems are assembled in the uppermost part of building structures to provide protection and insulation from external elements such as rain, sunlight, and heat. These roofing standards are helpful in guiding product manufacturers, construction companies, architectural firms, and other producers and end-users of these parts and components in their proper fabrication and installation, as well as the possible hazards involved during these procedures.
We will not be taking a deep dive into ASTM. However, when possible it is always best to purchase and install roofing products that have been tested and comply with ASTM Standards. All labels will clearly state if the product complies with ASTMand as to what test standard.
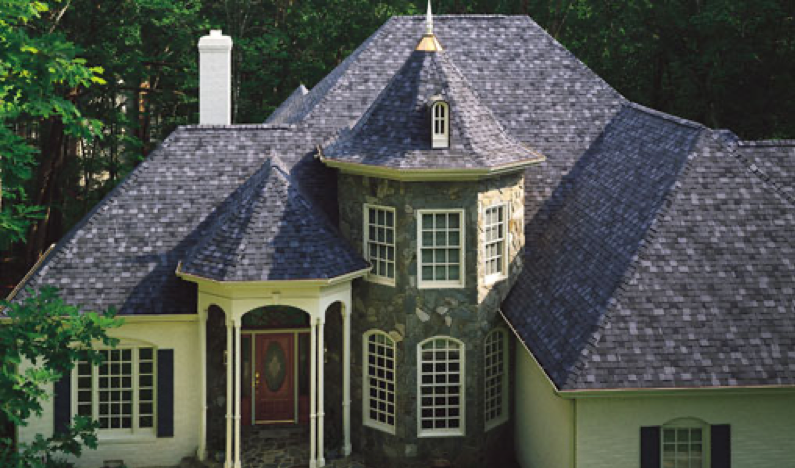
While each roofing products offers its own pros and cons, anyone of them can add a beautiful distinct look to home or building. After reading through this article, you will be well versed and make the decision that’s best for you.
Considerations of a New Roof
There are many considerations you should absolutely think about when selecting your new roof:
- How long should the roof last?
- Will it stand up to heavy winds and hailstorms?
- Is my structural framing capable of holding any additional weight?
- Is my roof properly sloped for the roofing material I want?
- How will the new roof look on my home or building?
- What type of roofing materials will be installed?
- Are there any building code, subdivision rules or colors not permitted?
- What’s my budget cost of not roofing or expense of new roofing?
- Will my Homeowners Insurance be affected?
Pros and Cons
Not all roofing material is created equal, and just because it’s a roofing product, certainly doent mean it should or could be used on your home or building. In most circumstances of premature roof failure, the wrong roofing product was chosen for the installation. Many factors such as the roof slope, building location, structural integrity and building use, need to be minimal questions to ask yourself prior to new roofing.
Areas prone to severe weather like severe winds, large hail, hurricanes and wildfires, should consider impact resistant and class A fire resistant products. (List Manufactures)
The following should help you in making a sound decision for your next roofing project.
Asphalt Composition Shingles
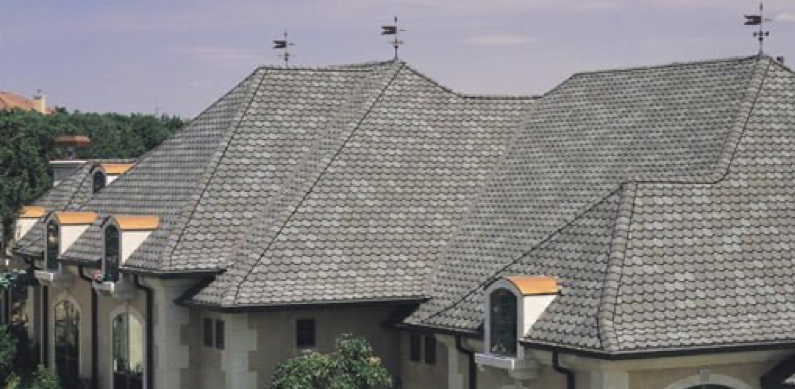
What are Asphalt Shingles are certainly the most popular choice for roofing of homes and commercial buildings today, comprising over 70% of roofing market, due to the economic benefit.
There are 3 Primary Roof Shingle Types;
According to Wikipedia:
Organic
Organic shingles are made with a base mat of organic materials such as wastepaper, cellulose, wood fiber, or other materials. This is saturated with asphalt to make it waterproof, then a top coating of adhesive asphalt is applied, covered with solid granules. Such shingles contain around 40% more asphalt per square (100 sq ft.) than fiberglass shingles. Their organic core leaves them more prone to fire damage, resulting in a maximum class “B” FM fire rating. They are also less brittle than fiberglass shingles in cold weather.
The early wood material-based versions were very durable and hard to tear, an important quality before self-sealing materials were added to the underside of shingles to bond them to the layer beneath. Also, some organic shingles produced before the early 1980s may contain asbestos.
Fiberglass
Fiberglass reinforcement was devised as the replacement for asbestos in organic mat shingles. Fiberglass shingles have a base layer of glass fiber reinforcing mat made from wet, random-laid glass fibers bonded with urea–formaldehyderesin. The mat is then coated with asphalt containing mineral fillers to make it waterproof. Such shingles resist fire better than those with organic/paper mats, making them eligible for as high as a class “A” rating. Weight typically ranges from 1.8 to 2.3 pounds/square foot.
Fiberglass shingles gradually began to replace organic felt shingles, and by 1982 overtook them in use. Widespread hurricane damage in Florida during the 1990s prompted the industry to adhere to a 1700-gram tear value on finished asphalt shingles[citation needed].
Per 2003 International Building Code Sections 1507.2.1 and 1507.2.2, asphalt shingles shall only be used on roof slopes of two units vertical in 12 units horizontal (17% slope) or greater. Asphalt shingles shall be fastened to solidly sheathed decks. Shallower slopes require asphalt rolled roofing, or other roofing treatment.
Architectural or 3-Tab
Asphalt Shingles come in two standard design options: Architectural (also known as Dimensional) Shingles, and 3-Tab Shingles. 3-Tab are essentially flat simple shingles with a uniform shape and size. They use less material and are thinner than Architectural Shingles, and are therefore lighter and lower cost for both the material and the installation. They also do not last as long or offer Manufacturer’s Warranties as long as good architectural asphalt shingles. 3-Tab are still the most commonly installed in lower-value homes, such as those used as rental properties. However, they are declining in popularity in favor of the architectural style. Dimensional, or architectural shingles are thicker and stronger, vary in shape and size, and offer more aesthetic appeal; casting more distinct, random shadow lines better mimics the appearance of traditional roofing materials such as wood shake shingles.[6] The result is a more natural, traditional look. While more expensive to install, they come with longer manufacturer’s warranties, sometimes up to 50 Years – typically prorated, as virtually all asphalt shingle roofs are replaced before such an expiration could be reached. While 3-tab shingles typically need to be replaced after 15–18 years, Dimensional typically last 24–30 years.
So now you Know that Roofing Shingles
- Roofing Shingle Materials are typically made of organics papers or fibers and seem to perform better in high wind and colder climates. Fiberglass shingles are better for fire and moisture resistance. Both products are asphalt impregnated and coated with embedded granules. Not all granules are embedded in asphalt but are interlocked to other granules.
- Appearance: Traditional 3-tab shingles or thicker laminated architectural or dimensional shingles. Roofing Shingles will lay flat and conform to most surfaces.
- Partially Eco-Friendly: Most roofing shingles be recycled, and used in highways, landscaping and other projects. Hence reducing the what’s delivered to landfills
- Durability: Not all shingles are durable. Impact resistant and Algae-resistant shingles are available in most states.
- Weight: Moderate in weight, ranging from 180lbs per square to 400 lbs per 100 square feet.
- Slope: Slope considerations must be taken into account on all roof structure types. Especially the low slope and then to the steeper-sloped roofs.
- Fire & Wind: Class A and B fire resistance available, fair wind resistance.
- Cost: Inexpensive to moderate for designer shingles.
What is roofing felt?
To understand what underlayment might be best for you. It will be important for you to know what roofing felt is. Roofing felt is essentially a polyester, cotton or fiberglass fleece that is soaked in some type of waterproofing agent. It is available in two thicknesses,15 and 30 pounds with two different manufacturer standards. One complies with ASTM 4869 and the other doesn’t. Don’t be fooled. The product that complies to the ASTM 4869 standard is a superior product, the other is junk, and is typically sold at most lumber yards and big box stores. Non-ASTM complying felt can be dangerous to install on steep roofs. It will most likely wrinkle and never lay flat and needs to be covered the day its applied otherwise you may experience a wrinkled finished roof product.
The 15 and 30 numbers are a reference to how much 100-square feet of the paper used to weigh back in the early days of its use. The actual weight-per-square foot today is typically less than the label says, however the 15 pound. and 30 pound. Name stuck. Roofing felt typically comes in 36-inch wide rolls. !5 pound felt is a 400 square foot roll and 30 pound is a 200 square foot roll.
What is synthetic underlayment?
Different types of synthetic underlayment have been around since the early 2000’s. Most synthetics are woven or spun from either polyethylene or polypropylene. While the ingredients are similar, the manufacturing process and thickness of each type of underlayment can be fine-tuned to produce different properties, such as exposure time and walkability. One way of comparing synthetic underlayment is by weight, similar to the way that felt is compared. Instead of pounds-per-100-square-foot, synthetics are rated by grams-per-square-meter (GSM).
Types of roofing material matter
Not all types of roofing can be installed over all types of synthetic underlayment. When installing any kind of roofing other than asphalt (steel, wood, tile, etc.), make sure the synthetic you install is compatible.
Don’t skip peel and stick
Synthetic underlayment still needs to be used in conjunction with peel and stick (aka. self-adhering or ice and water) underlayment, which are required to cover overhangs, valleys and wall intersections. There are synthetic peel-and-stick products available, but they are not as widely used because they are seen as most contractors as cost prohibitive. Roofing codes vary from region to region; make sure to check with your local building officials on the peel and stick requirements in your area.
Ice and Water Shield
Ice and Water Shield, sometimes also referred to as Moisture Barrier, is a waterproof roof underlayment membrane developed to protect vulnerable areas on a roof from ice and water damage. Ice and Water Shields are made with polymer-modified bitumen. The adhesive back surface of the membrane will bond to the roof deck, which is a superior underlayment for areas where ice dams or severe storms are common.
What’s overlooked in Underlayment Installation
Other than buying a product that complies with ASTM standards is fastening the product. Most shingle manufactures have very fine line warranty or guarantees, and the slightest mistake can void your warranty. 2018 Building codes now require for underlayment to be fastened with a required fastener. See building code below
R905.1.1
Underlayment (Source IRC 2018)
Underlayment
for asphalt shingles, clay and concrete
tile, metal roof shingles,
mineral-surfaced roll roofing, slate and slate-type shingles, wood shingles,
wood shakes and metal roof panels
shall conform to the applicable standards listed in this chapter. Underlayment
materials required to comply with ASTM D226, D1970, D4869 and D6757 shall bear
a label indicating
compliance to the standard designation and, if applicable, type classification
indicated in Table R905.1.1(1). Underlayment
shall be applied in accordance with Table R905.1.1(2). Underlayment
shall be attached in accordance with Table R905.1.1(3).
The underlayment
shall be attached with
corrosion-resistant fasteners in a grid pattern
of 12 inches between side laps with a
6-inch spacing at the side laps.
Underlayment
shall be attached using
metal or plastic cap nails or cap staples with
a nominal cap diameter
of not less than 1
inch. Metal caps shall have a thickness of
not less than 32-gage sheet metal. Power-
driven metal caps shall have a minimum
thickness of 0.010 inch. Minimum thickness
of the outside edge of plastic caps shall
be 0.035 inch. The cap nail shank shall be
not less than 0.083 inch for ring shank cap
nails and 0.091 inch for smooth shank cap
nails. Staples shall be not less than 21 gage.
Cap nail shank and cap staple legs shall
have a length sufficient to penetrate through
the roof sheathing or not less than 3/4
inch into the roof sheathing.
Roof Ventilation
Installing Roof Vents: What You Need To Know
Please note: The below information and instructions are for the general information and are not intended to be relied upon as specific advice for a particular roof.
An important part of a healthy home, and a complete roofing system, is roof vents.
The installation of roof vents is a crucial part of roof design because it allows for proper attic ventilation, which may help prevent condensation and early aging of your roofing materials.
Advantages Of Proper Roofing Ventilation
Although there are many different types of roof vents to choose from, ensuring you have the right number of both intake and exhaust vents is a central part of roof design. Proper attic ventilation offers numerous advantages to the homeowner:
• As the ventilation helps moderate the temperatures in the attic, this may also help moderate the temperature in the rest of the home
• It helps prevent moisture buildup in your attic, which, during colder months, can help prevent condensation issues that can affect the materials in the attic space, especially insulation.
• By preventing excess heat buildup, proper ventilation promotes energy efficiency in the home, so your heating costs may be lower
• It helps protect the life of the roofing materials (condensation is a leading cause of damage to roofing materials, such as asphalt roofing shingles)
• It helps you remain compliant with most local building codes, which often require proper attic ventilation in homes
Sources: (Air vent, NRCA, Professional Roofing)
How To Calculate The Amount Of Ventilation You Need
Please note: the following provides advice for homes with ventilated attics. There are some styles of vaulted ceiling homes or flat roof homes that have ventilation spaces within the roof itself, and no attic. These ventilation needs are calculated differently.
The key to proper ventilation of your roof and attic is balance: the amount of space you devote to intake must be equal to the amount you allow for exhaust, and these must be calculated according to the size of your attic and slope of your roof.
You can calculate attic ventilation requirements by determining the square footage of your attic floor (its width times its length), and compare that to the total required “net free area” (NFA). Vents are rated by their net free area, or the amount of space for air to flow in or out. This helps make it easy to calculate how many vents you need for your attic, once you’ve determined your requirements.
If your attic floor has a vapor barrier, you will need one square foot of NFA per every 300 square feet of attic floor area (half of that will be intake, half for exhaust). If there is no vapor barrier, double it to one square foot of NFA for every 150 square feet of attic floor space (half for intake, half for exhaust). These are broad guidelines, so be sure to check with your local building code.
Source: (NRCA Stanley Complete Roofs and Siding, Airvent.com)
Also, the NFA will be calculated differently if your roof slope is greater than average. If the slope of your roof is greater than 6:12 you will need more ventilation to reflect the extra volume of attic space: Calculate 20 per cent more for 7:12 to 10:12 pitches, and 30 per cent more for a pitch that is 11:12 or greater.
(Source: Asphalt Roofing and NRCA.)
Metal
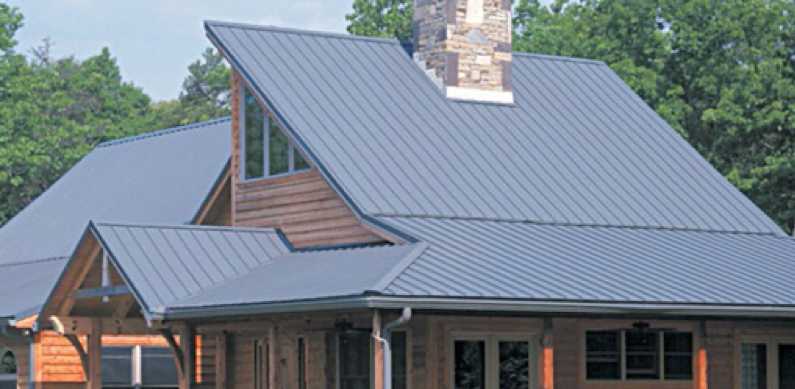
While more expensive than asphalt shingles. Metal Roofing lasts up-to three times as long as shingle roofs.
- Materials: May be composed of steel, aluminum, copper, or zinc alloy. Steel roofs come with either a zinc coating or painted finish. Copper roofs are installed unfinished and acquire a protective green patina with age.
- Installation: When choosing a metal roof, there are several options to consider. First and foremost, is to be certain that the contractor is qualified to install the roof to the manufacturer’s specifications. Keep in mind that residential metal roofing is a rapidly growing industry. As such, there are individuals on the supply and installation end of things who may not be as well informed of products and their limitations, as they should be. A metal roof is a considerable and crucial investment in a home – do not leave things to chance. The installers of your roof should be an experienced factory trained and certified installers. Go look at past jobs they have installed and talk with their references before making a final decision.
- Profiles: Metal roof coverings can be, Shake, Shingle, Tile, Slate with many different profile types. There are literally dozens of different “looks” and “feels” that can be achieved with metal roofing – from the traditional, sleek standing seam look, to the old-world tile look, to the more agricultural corrugated look. The variety of attractive metal roofing profiles is one of the great advantages offered by the industry. No matter what the style or look of your home, there is almost certainly a metal roof system out there that will complement it perfectly! Unfortunately, the variety of profiles sometimes turns out to be one of the industry’s detriments as well, because it can lead to improper products being used for less than ideal applications
- Eco-Friendly: May be made from recycled materials and can be recycled when replaced. Absorb a third less heat than asphalt.
- Underlayment: Most Metal Roofing requires a specific type of underlayment. The roof slope/pitch. Type of metal used, and other factors will be determining factor for this.
- Durability: Fairly to very durable, depending on the material.
- Weight: Lightweight.
- Slope: Available for low (you will want to verify your choice product against the required roof slope) or steep sloped roofs.
- Fire & Wind: Good resistance to both fire and wind.
- Cost: Moderate (steel) to the very high end (copper).
- Extremely Important note. Some insurance carriers exclude certain coverages on metal roofing. There typical exclusions will include denting, marring and cosmetic and functional damage. You certainly need to discuss this with your insurance agent. You do not want to spend thousands on a beautiful roof to only find out you may have limited coverage in the event of a covered or uncovered insurance peril.
Plastic Polymer-Synthetic Roofing
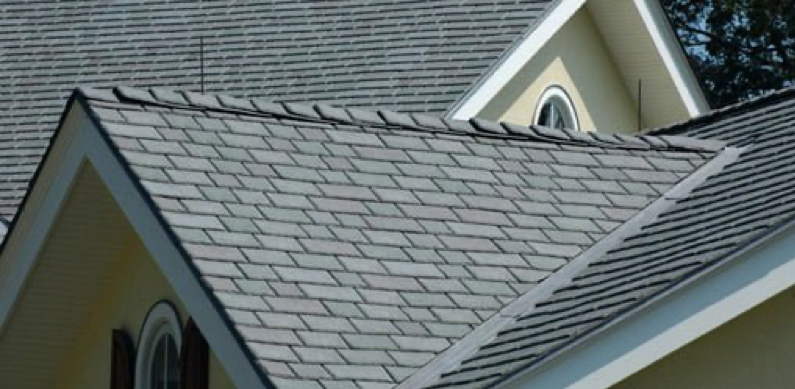
These durable synthetic roofing shingles resemble either wood, shakes or slate. Synthetic roofing tiles provide a high-performance option for homeowners. The tiles come in a variety of styles, including slate and shake, are lightweight and have long-term durability. These tiles are moderately priced and a good environmental choice. While the look complements many home styles, synthetic roofing tiles are moderately priced, so they’re affordable for everyone.
- Materials: Molded from a high-tech plastic polymer material, which is impregnated with fire retardant and state of the art advanced UV stabilizers specifically formulated for the tough conditions that roof tiles are exposed to in all climates throughout the year.
- Appearance: Made to resemble slate or wood shakes.
- Durability: Claimed to be long-lasting and low maintenance. Synthetic roofing tiles last up to 50 years and require minimal maintenance attention.
- Eco-Friendly: Some are made from recycled materials. Can be recycled when replaced.
- Weight: Light to moderate in weight.
- Slope: Can be used from low slope to steep-sloped roofs.
- Fire & Wind: Good fire and wind resistance.
- Cost: Moderate to High-end.
Tile
Clay Tile
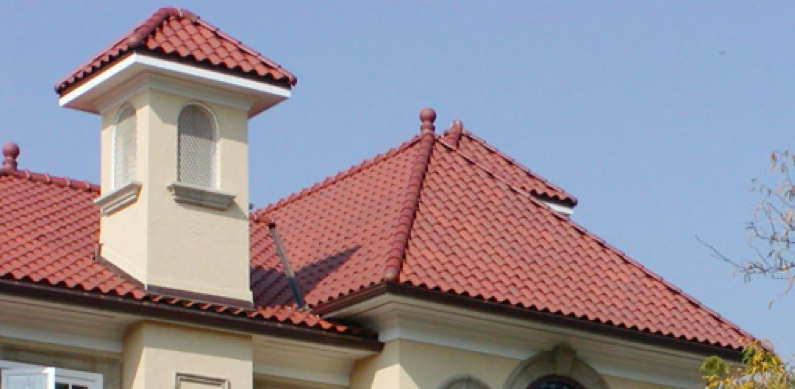
While brittle and heavy, clay tiles can last a long time and are very fire resistant.
- Materials: Made from natural clay which is fired in a kiln.
- Appearance: Traditional Italian or Spanish look, can also be made to resemble wood shakes or slate.
- Eco-Friendly: Made from natural materials but requires significant energy to manufacture.
- Durability: Long-lasting and low maintenance but brittle and can break.
- Weight: Heavy, require reinforced roof framing to support.
- Slope: Can be used on moderate to steeper-sloped roofs.
- Fire & Wind: Excellent fire resistance, fair to low wind resistance.
- Cost: Expensive.
Concrete Tile
Less expensive than clay tiles, concrete roof tiles are also heavy but can last a long time and are very fire resistant.
- Materials: Made from a mixture of Portland cement and sand.
- Appearance: Can be made to resemble traditional clay tiles, wood shakes, or slate. Color can be throughout tile or only applied on the surface.
- Eco-Friendly: Made from natural materials but requires significant energy to manufacture.
- Durability: Long lasting and low maintenance but can break.
- Weight: Heavy, require reinforced roof framing to support.
- Slope: Can be used on moderate to steeper sloped roofs.
- Fire & Wind: Excellent fire resistance, fair to low wind resistance.
- Cost: Moderate.
Slate
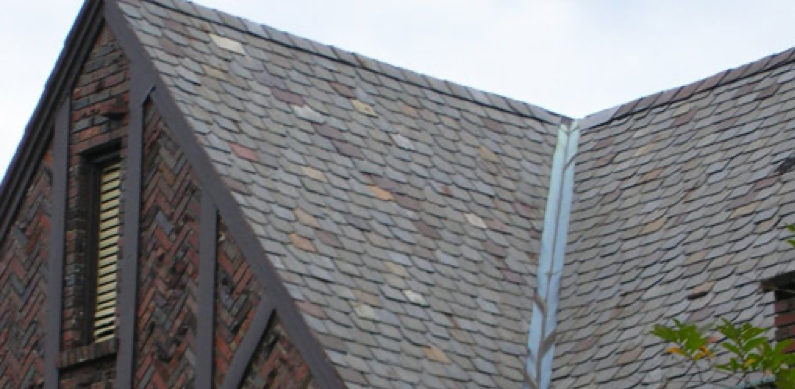
Slate is one of the oldest roofing materials. Though brittle and expensive, it is very durable and resists both wind and fire.
- Materials: Made from natural slate rock.
- Appearance: Usually dark gray with irregular appearance.
- Eco-Friendly: Made from natural materials.
- Durability: Long lasting, durable (depending on where quarried).
- Weight: Heavy, require reinforced roofing structure to support.
- Slope: Steep sloped roofs only.
- Fire & Wind: Good fire and wind resistance.
- Cost: Very expensive. Requires specially trained workers to install.
Wood Roofing Types
Wood Singles and Shakes
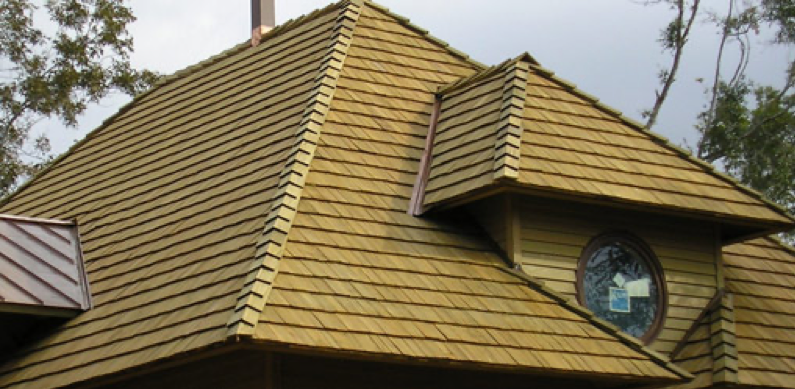
Wood shingles and shakes made from rot resistant woods have low fire resistance unless treated.
- Materials: Commonly made of cedar, but can also be made of other rot resistant woods, such as redwood.
- Appearance: Gives natural look, weathers to a silvery gray. Available in sawn shingles or thicker split shakes.
- Eco-Friendly: Made from natural materials.
- Durability: Short lifespan and requires periodic maintenance.
- Weight: Moderate in weight.
- Slope: Can be used on moderate to steep sloped roofs.
- Fire & Wind: Good wind resistance, poor fire resistance (can be treated with a fire retardant).
- Cost: Moderate.
Flat Roof Chart “Bur” Built up Roofing
Tpo Membrane
Pvc Membrance
SBS Modified
Hot Mopped Multi Ply
Cold Applied Multi Ply
Roof Coatings
No representation, warranty or guarantee is made as to the Technical Data Sheet’s accuracy or completeness.